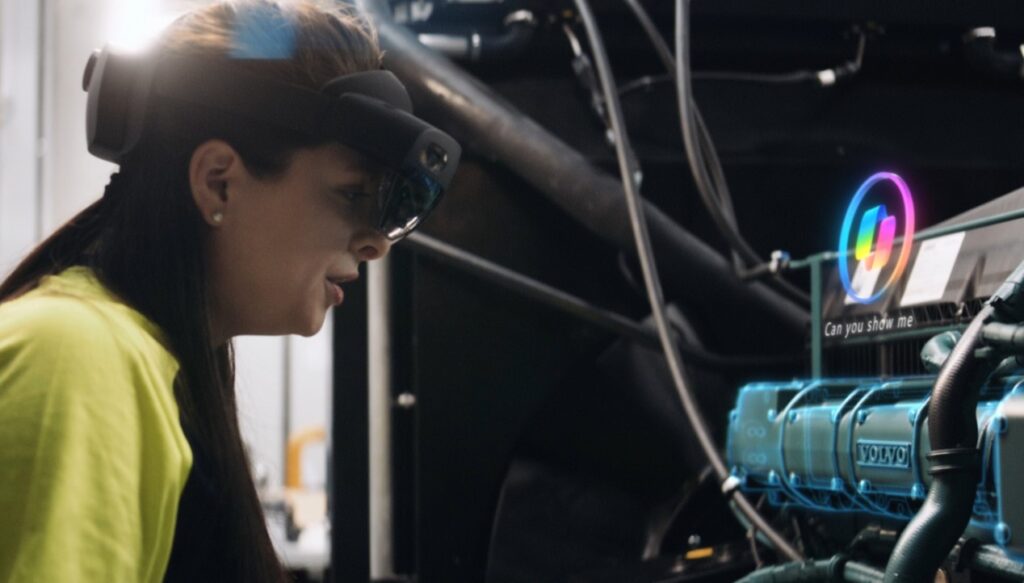
Early adopters of Microsoft Copilot in Dynamics 365 Guides recognize the potential for productivity gains
In this era of rapid technological advancement, our industrial landscape is undergoing a significant transformation that affects many processes and people—from the way operational technology (OT) production data is leveraged to how frontline workers perform their jobs. While 2.7 billion skilled individuals keep manufacturing operations going, their attrition and retirement rates are on the rise. This heightened turnover is contributing to an ever-widening skills gap, pressuring organizations to look beyond traditional working and skilling to extend capabilities and ensure growth.
Microsoft developed Dynamics 365 Guides to address these challenges. The integration of Microsoft Copilot into Guides brings generative AI to this mixed reality solution. Copilot in Dynamics 365 Guides transforms frontline operations, putting AI in the flow of work, giving skilled and knowledge workers access to relevant information where and when they need it. This powerful combination—mixed reality together with AI—provides insight and context, allowing workers to focus on what truly matters.
Generative AI represents an enormous opportunity for manufacturers
With 63% of workers struggling to complete the repetitive tasks that take them away from more meaningful work, many are looking eagerly to technology for assistance. Generative AI addresses these realities by equipping skilled assembly, service, and knowledge workers with the information necessary to keep manufacturing moving. Integrating Copilot into Guides furthers Microsoft’s commitment to this underserved group within enterprises. Workers are using Copilot in Dynamics 365 Field Service to complete repair and service work orders faster, boosting overall productivity. Copilot is already creating efficiencies for organizations worldwide, though still in private preview, we’re excited to see how Guides unlocks frontline operations and use cases.
Copilot makes information and insight readily available. Generative AI enables Guides to put these details in context against neighboring machine components and functions, enabling technicians to repair and service faster. Copilot removes the guesswork or need to carry around those dusty old manuals. Users can ask questions using their natural language and simple gestures. Copilot summarizes relevant information to provide timely virtual guidance overlaid on top of their environment.
Manufacturers will see this innovation firsthand at Hannover Messe 2024. Partnering with Volvo Penta and BMW Group, Microsoft will illustrate generative AI’s potential on service and manufacturing frontlines. Read what we have planned at Hannover with Volvo and BMW, and what other private preview customers are doing with Copilot.
Volvo Penta is focused on transforming training in the field
Volvo Penta, a global leader in sustainable power solutions, is always looking for ways to utilize new technology to increase efficiency and accuracy and has recently been utilizing augmented reality (AR) capabilities that enhance worker training and productivity. As an early adopter of Guides and Microsoft HoloLens 2, Volvo Penta was eager to participate in the private preview for Copilot in Dynamics 365 Guides. For Volvo Penta, Copilot is another technology with the potential to unlock further value for their stakeholders.
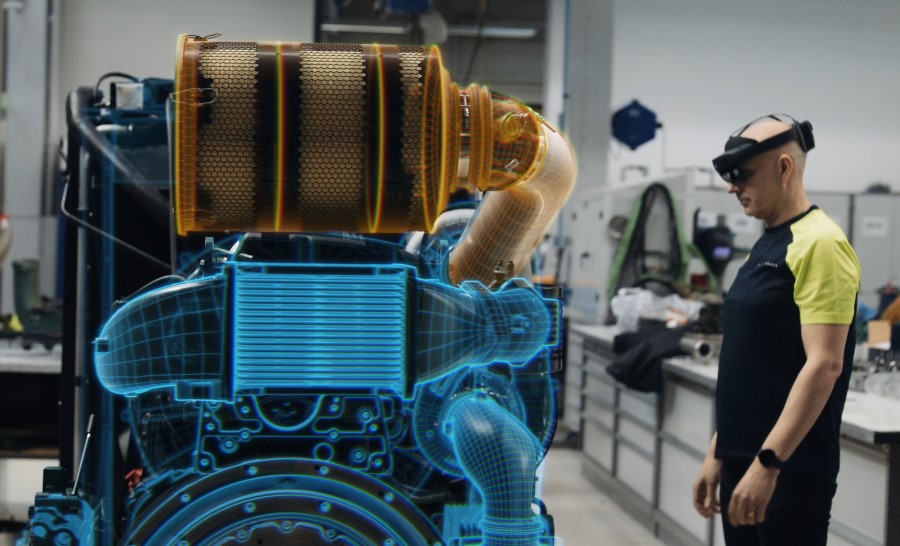
Volvo Penta is part of a conceptual innovation exploration, to evaluate how Copilot can help optimize the training of entry-level technicians by enhancing self-guided instruction. As Volvo Penta’s Director of Diagnostics put it, “Copilot makes it feel as though a trainer is always on hand to answer questions in the context of your workflow.” Locating 10 to 15 sensors used to take new technicians an hour or more, and now it only takes five minutes. This time savings has the potential to significantly increase productivity and learning retention, helping Volvo Penta, its customers, and dealers, accomplish more. The company continues to innovate with AI and mixed reality solutions to modernize service and streamline frontline operations.
At Hannover Messe 2024, the company is showcasing how Copilot could serve their customers to improve uptime and productivity. In the demo scenario, Volvo Penta envisions its ferry captains using Copilot to address a filter issue prior to departure. Left without a service technician onboard, the captain troubleshoots replacing the filter, using Copilot and HoloLens 2 to do so with step-by-step guidance.
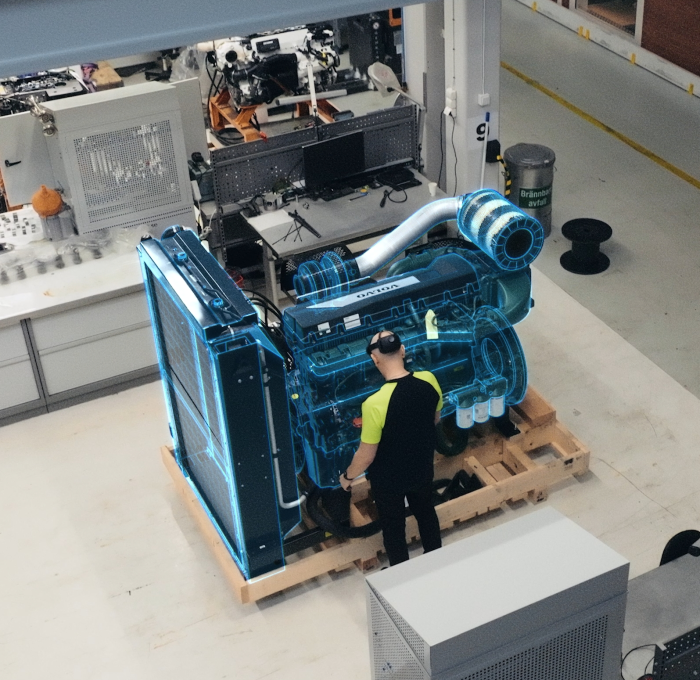
Volvo Penta
See how Volvo Penta streamlines frontline operations with Copilot in Dynamics 365 Guides
BMW Group is pushing the boundaries of vehicle design and development
BMW Group is improving its product lifecycle, incorporating generative AI, human-machine interactions, and software-hardware integrations for better predictability, optimization, and vehicle innovation. As a global HoloLens 2 customer, BMW Group has spent the last couple years developing its own immersive experiences and metaverse using mixed reality. Now participating in the private preview for Copilot in Dynamics 365 Guides, they are exploring how the combination of mixed reality and generative AI, together, can push the boundaries of innovation.
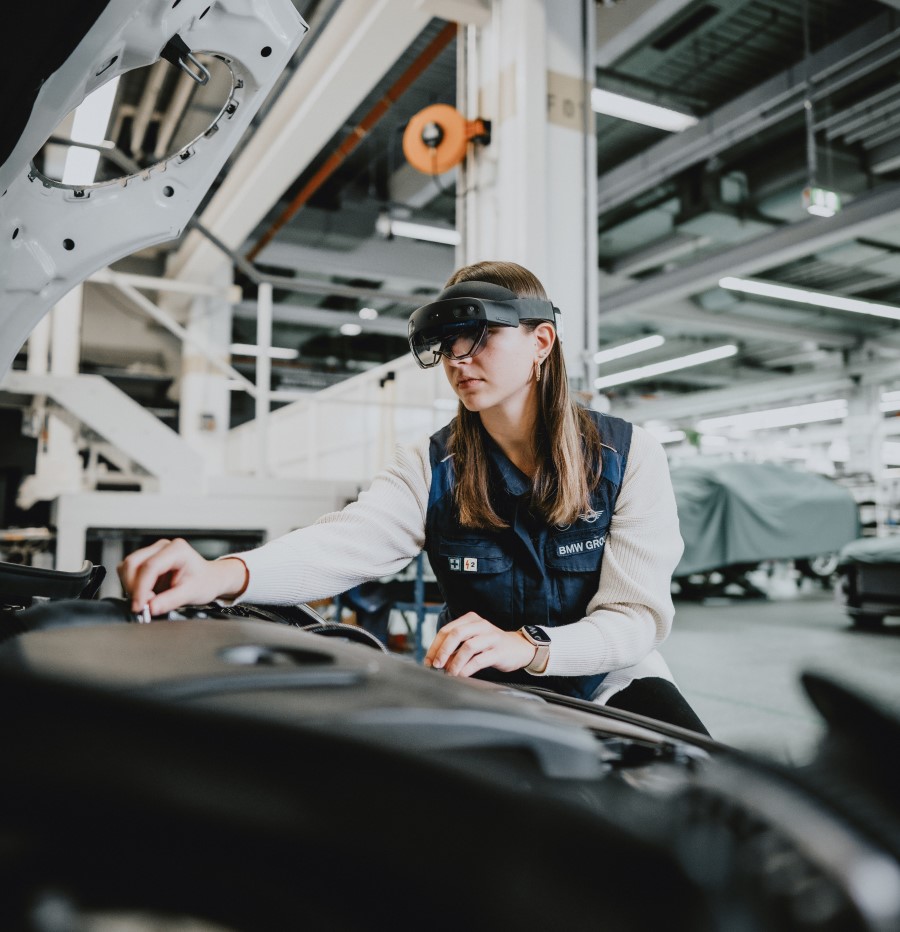
In private preview, BMW Group’s Digitization and virtual reality (VR) Team within research and development (R&D) is the first to evaluate Copilot’s potential on design and development. With Copilot, product designers and engineers are simulating how the use of different materials and components impact vehicle design and their environmental footprint. The insights gained through this approach will help BMW Group optimize engineering and production processes. The organization believes generative AI will also benefit its Aftersales frontline workers, providing them access to expert knowledge and guidance, whenever and where it is needed.
This joint collaboration will ultimately enable BMW Group to spark innovation and target the use cases that drive its own digital transformation forward.
Chevron is exploring the potential impact on frontline operations
AI, automation, and mixed reality solutions are poised to reshape industries everywhere. Within energy, a focus on safety and the desire to accelerate skilling has Chevron looking to advance the capabilities of its frontline workers for the future. Copilot in Dynamics 365 Guides offers Chevron the opportunity to optimize these operations, empower its workers, and infuse informed decisions throughout its value chain. AI and mixed reality, together enables Chevron to define energy in human terms.
Through the private preview for Copilot in Dynamics 365 Guides, Chevron is exploring new use cases at its El Segundo Refinery that could unlock further enhancements in worker skilling and safety.
Get started with Copilot in Dynamics 365 Guides
Interested customers can get started by deploying Dynamics 365 Guides and Dynamics 365 Remote Assist on either HoloLens 2 or mobile devices as the first step. If you want to see how AI can transform your workforce, learn how you can start implementing Microsoft Copilot today.